Los orígenes de la gestión de proyectos lean
La historia de Lean comienza después de la Segunda Guerra Mundial. La devastación de Japón durante la guerra generó escasez de equipos y recursos, y los fabricantes debieron inventar formas de prosperar en un nuevo entorno económico. Estados Unidos envió asesores a Japón para ayudar a los fabricantes del país a reconstruir sus capacidades de producción. Uno de estos expertos fue W. Edwards Deming, consultor de gestión cuyas ideas sobre el control de calidad encontraron audiencias más receptivas en Japón que en los Estados Unidos.
De estos asesores, así como de las visitas a Ford y las cadenas de supermercados estadounidenses, los fabricantes japoneses y Toyota, en particular, perfeccionaron el concepto de justo a tiempo (JIT). Esta técnica tiene como objetivo aumentar la eficiencia y reducir la cantidad de inventario almacenado moviendo los materiales a su posición justo antes de que sean necesarios para la siguiente etapa del proceso de producción. JIT no se utiliza únicamente en la fabricación; la técnica se aplica en cualquier situación en la que un proveedor entrega materiales utilizando un cronograma determinado por la demanda del cliente. El éxito de JIT depende de la capacidad de sincronizar y coordinar los pasos del proceso de fabricación para que los materiales y los productos estén donde necesitan estar, cuando necesiten estar allí.
En la década de 1950, JIT, en combinación con el método de fabricación japonés de Jidoka o autonomía (automatización con un toque humano con excepciones) se convertiría en los dos pilares del Sistema de Producción de Toyota (TPS). Muchos consideran al ingeniero de Toyota, Taiichi Ohno, el padre del TPS y Lean. El TPS estaba orientado a satisfacer las necesidades de los mercados japoneses en ese momento, lo que pedía una cantidad menor de varios tipos de vehículos diferentes. Su principio central era la eliminación sistemática de residuos en un esfuerzo continuo por mejorar la eficiencia.
Un par de décadas más tarde, luego de que el embargo petrolero árabe de 1973 causó crisis energéticas en Estados Unidos, Japón, Canadá, Reino Unido y los Países Bajos, otras empresas japonesas empezaron a estudiar e imitar el TPS. Por ahora, los beneficios del TPS estaban claros. Aportó:
- Tiempos de entrega reducidos
- Menores inventarios
- Disminución de los costos
- Mejora de la productividad
- Mayores márgenes de ganancias
- Aumento de la calidad del producto
- Mayor satisfacción del cliente
Los conceptos de Muda, Muri y Mura (tres tipos de residuos que se conocen como 3M) son fundamentales para la idea de eliminar los residuos. Muda se refiere a las actividades que consumen recursos sin aumentar el valor final entregado al cliente. Muri se refiere a prácticas que implican el uso excesivo del equipo o la sobrecarga de trabajo de los empleados más allá de límites razonables o prácticos, que aumentan los costos y reducen la eficiencia y la productividad a largo plazo. Mura describe la "desigualdad" operativa, que se puede considerar como el rendimiento irregular del trabajo que aumenta los costos y posiblemente reduce la eficiencia con el tiempo.
Guía para la gestión de proyectos
Su ventanilla única para todo tipo de gestión de proyectos
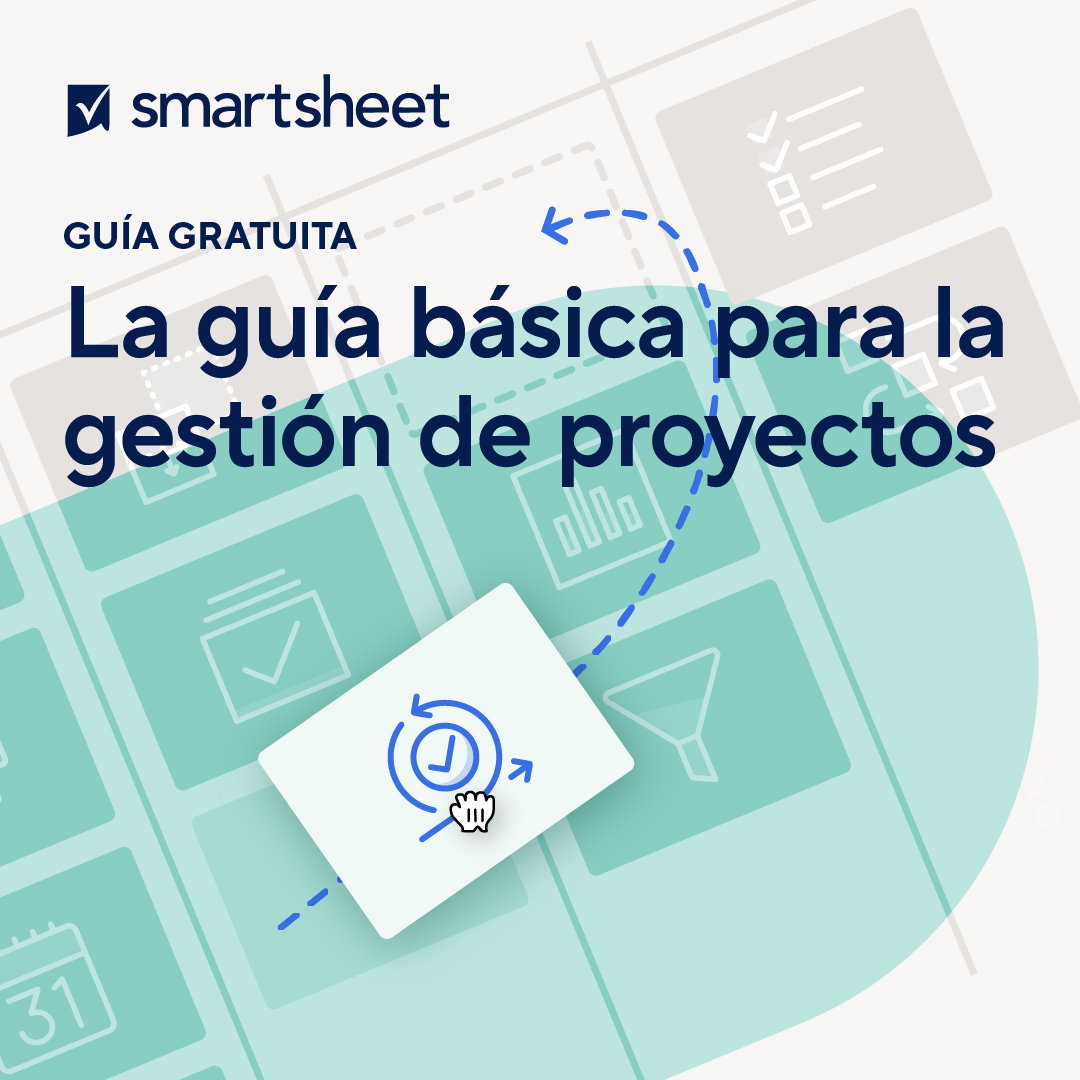
¿Está listo para sacar más provecho de sus esfuerzos de gestión de proyectos? Visite nuestra guía completa de gestión de proyectos para obtener consejos, prácticas recomendadas y recursos gratuitos para gestionar su trabajo de manera más efectiva.
Lean migra de Japón a Occidente
En la década de 1980, los fabricantes occidentales descubrieron que las empresas japonesas las estaban superando. Intentaron emular el TPS, empleándolo bajo nombres como Fabricación de clase mundial, Producción sin existencias y Fabricación de flujo continuo. Los fabricantes también empezaron a implementar algunas de las técnicas de fabricación Lean, aunque aisladas de la filosofía general de gestión de negocios.
En 1988, John Krafcik, un estudiante de MBA convertido en ingeniero de calidad, escribió un artículo que comenzó un cambio de paradigma en la fabricación estadounidense. Krafcik, quien había trabajado en New United Motor Manufacturing, Inc. (NUMMI), una empresa de fabricación de automóviles propiedad conjunta de GM y Toyota, publicó Triumph of the Lean Production System basado en su tesis de maestría en el MIT. Los académicos del Programa Internacional de Vehículos a Motor del MIT continuaron su investigación sobre la producción Lean.
En 1990, tres eruditos, James P. Womack, Daniel T. Jones y Daniel Roos publicaron un bestseller internacional, The Machine that Changed the World, que desempeñó un papel sumamente importante en la difusión del concepto de fabricación Lean en occidente. En ese libro y Lean Thinking, se presentaron los principios de Lean de una manera que permitía a los fabricantes occidentales comprender la extensión total de sus beneficios.
Pensamiento Lean: The Spread of Lean’s Influence
Los principios de la fabricación Lean, ahora más ampliamente conocidos como Pensamiento lean, se han adoptado desde entonces fuera de la fabricación tradicional en campos como la construcción, la salud, los servicios financieros, el gobierno, la gestión de proyectos y el trabajo del conocimiento. El uso de Lean para el trabajo del conocimiento se ha encontrado con algunas dudas y resistencia por parte de personas que argumentan que, dado que el campo es esencialmente no replicable y no repetitivo, no es adecuado para la estandarización. Bradley Staats y David M. Upton argumentan en Harvard Business Review, sin embargo, que todas las empresas especializadas en el trabajo del conocimiento llevarán a cabo actividades no basadas en el conocimiento que sean adecuadas para los esfuerzos de reducción de desperdicios. Además, incluso puede optimizar las secuencias de actividades básicas basadas en el conocimiento para lograr una mayor eficiencia.
Por ejemplo, piense en Kanban, una práctica de Toyota que usa ayudas visuales (como señales, tarjetas o notas adhesivas) para combinar el inventario con la demanda a lo largo del ciclo de vida de la producción. Esto hace que las ineficiencias del proceso, los cuellos de botella y otros tipos de desperdicios sean evidentes. Kanban se ha utilizado con éxito en el desarrollo de software, al visualizar el proceso de desarrollo de software como una cadena de producción, identificar posiciones y situaciones que causan ineficiencia en la cadena de producción e implementar soluciones para aumentar la eficiencia general de la cadena de producción.
Lean ha tenido una influencia generalizada. Por ejemplo, la Iniciativa Aeroespacial Lean fue un proyecto piloto financiado por la Fuerza Aérea de los Estados Unidos en 1992 en el MIT que estudió el uso de técnicas Lean en la fabricación de productos aeroespaciales. El proyecto fue renombrado como Iniciativa de Avance Lean hasta que se disolvió en 2012.
La salud, los servicios financieros, la educación, la venta minorista, la construcción y otros campos incorporan actualmente los principios de Lean basados en el TPS. Debido a que Lean es un paradigma que rige todo lo que hace una organización, en lugar de una sola táctica o iniciativa orientada a un resultado estrecho, se puede aplicar a diversos tipos de industria y organización.
En última instancia, las transformaciones Lean hoy en día se centran en cambiar el pensamiento de una organización para que optimice su propósito (proporcionar mayor valor al cliente), procesos (maximizar la productividad del flujo de trabajo) y personas (cómo el equipo puede involucrarse mejor en la mejora continua).
Aplicar Lean a la gestión de proyectos
Un artículo de conferencias del Project Management Institute de Aziz Moujib describe la gestión de proyectos Lean como la aplicación de los principios de fabricación Lean al proceso de gestión de proyectos. Esto es en un esfuerzo por lograr el mismo objetivo: maximizar el valor y minimizar el desperdicio. Se basa en un conjunto de cinco principios básicos identificados en el libro Lean Thinking: Banish Waste and Create Wealth in Your Corporation, escrito por dos de los tres autores del MIT que escribieron The Machine that Changed the World.
El concepto del flujo de valor es fundamental para la gestión de proyectos Lean. Esta es la secuencia de actividades involucradas en la entrega de un proyecto con un valor acordado (tanto los aportes como los resultados). La asignación de flujos de valor, a veces llamado asignación de procesos de negocios, es un esfuerzo por comprender cómo se crean el valor y el desperdicio durante el ciclo de vida del proyecto con el objetivo de optimizar el flujo de valor. Al hacerlo, la gestión de proyectos Lean puede ayudar a alcanzar una serie de objetivos, como:
- Mejorar la calidad del producto final
- Completar el proyecto a tiempo y reducir el tiempo hasta su finalización
- Completar el proyecto sobre el presupuesto y cumplir con los requisitos de rendimiento del proyecto
- Eliminar el desperdicio
- Reducir costos
- Agregar valor
La estandarización es otro aspecto crítico de la gestión de proyectos Lean. Dado que la mayoría de los proyectos son novedosos (en cierta medida), la estandarización de las tareas puede mejorar el rendimiento del proyecto a corto plazo y ayudar a mejorar la eficiencia de los proyectos con tareas similares a largo plazo. La mejora de las tareas en el ciclo de vida del proyecto tiende a ser gradual, lo que conduce al progreso gradual hacia los objetivos.
Los cinco principios básicos del pensamiento Lean
La adopción del pensamiento Lean debe mucho a cómo se le presentó a James P. Womack y Daniel T. Jones, los autores de The Machine that Changed the World y Lean Thinking. Womack y Jones definieron cinco principios básicos del pensamiento Lean:
Comprender el valor: El primer principio hace hincapié en comprender el valor (o el servicio) de un producto a los ojos del cliente. La cantidad que un cliente está dispuesto a pagar por un producto o servicio está directamente relacionada con cuánto lo valora, por lo que comprender el valor de un producto es el primer paso hacia la fijación de precios efectiva y la gestión Lean. Toyota, por ejemplo, adoptó un enfoque descendente de precios definido por la cantidad de clientes que estaban dispuestos a pagar por un producto con determinado valor y, luego, se centró en eliminar el desperdicio de sus procesos de fabricación para cumplir con este precio.
Asignar el flujo de valor: El flujo de valor es la secuencia completa de actividades involucradas en la entrega de un producto final con un valor acordado y la asignación del flujo de valor significa usar técnicas de visualización como Kanban, diagramas de flujo o diagramas de espagueti para representar este flujo.Toyota fue pionero en la técnica de asignación de flujos de valor, que permite a los gerentes de negocios y estrategas identificar partes del flujo de valor donde se produce el desperdicio, y optimizar el flujo de valor para reducir el desperdicio. Un diagrama de espaguetis es un excelente punto de partida porque documenta visualmente el flujo real de producto, papel y personas en un lugar de trabajo o flujo de trabajo de un proyecto. Utilice la plantilla para crear su propio diagrama de espaguetis a continuación.
Descargar Plantilla del mapa de espagueti
Los expertos recomiendan crear un mapa de flujo de valor con lápiz y papel y documentar todos los pasos del proceso por los que pasa su producto, desde el proveedor hasta la organización y, por último, el cliente.
Asegurarse de que el flujo de valor fluye: El objetivo final de la asignación de flujos de valor es la preservación y optimización del flujo, la tasa y la "paridad" con la que los elementos y la información avanzan a través del flujo de valor. Este es el principio de la fabricación JIT en acción: debido a que el inventario excesivo, anticipado o inesperado genera desperdicios, la sincronización es la clave para optimizar el flujo. Identificar y eliminar el trabajo que no aporta ningún valor (ni directa ni indirectamente) también puede mejorar el flujo de un flujo de valor.
Emplear un enfoque Pull: La fabricación tradicional empleaba un enfoque Push en el que los objetivos de producción se definen en función de un cronograma y una cuota de producción determinados internamente. Este enfoque no responde muy bien a la demanda del cliente y, por lo general, llevó a que la producción superara o no cumpliese con la demanda. En el primer caso, tendría que almacenarse el producto excedente; en la segunda, tendría que aumentarse la tasa de producción, posiblemente más allá de los niveles óptimos de eficiencia, para satisfacer la demanda. De cualquier manera, este enfoque crea un montón de desperdicio innecesario.
En cambio, un enfoque Pull permite que la demanda del cliente determine la producción, de modo que no se crea nada a menos que un cliente lo solicite. Si se hace correctamente, se eliminan los desperdicios causados por los costos de inventario y la sobrecarga de trabajo. Sin embargo, un enfoque Pull es difícil de implementar de manera eficaz porque se basa en una evaluación precisa y efectiva del mercado y en la capacidad de variar la producción rápidamente y según la demanda. La entrega debe ser rápida para garantizar que la demanda del cliente siga existiendo cuando el producto final esté listo. Por último, un enfoque de extracción también requiere una coordinación altamente efectiva de la información en todo el flujo de valor, para que todos sean conscientes de los requisitos de producción y no surjan ineficiencias debido a la confusión y a las expectativas mal cumplidas.
Perseguir la mejora continua: En esencia, la gestión Lean es un proceso continuo e incremental. Un sistema sin desperdicios puede ser prácticamente inalcanzable, pero como objetivo, impulsa la necesidad de mejorar constantemente. La palabra japonesa Kaizen se utiliza a menudo para describir esta práctica en Lean. Con Kaizen, el flujo de valor se optimiza continuamente y los procesos defectuosos se mejoran o reemplazan constantemente en un esfuerzo por mejorar la calidad.
Otros principios clave en el desarrollo de software Lean incluyen amplificar el aprendizaje, decidir lo más tarde posible, entregar lo más rápido posible y potenciar al equipo.
Los pensadores lean se obsesionan con el desperdicio
Como hemos comentado, eliminar el desperdicio es el enfoque central de Lean. El desperdicio en la fabricación o construcción es fácil de visualizar: recursos no utilizados, esfuerzo innecesario, tal vez rechazo o productos secundarios. Sin embargo, para un trabajo que no implica un producto final físico, el desperdicio puede ser un poco más difícil de visualizar. ¿Qué tipo de desperdicio se imaginas, por ejemplo, de un proyecto de desarrollo de software?
Resulta que el concepto de desperdicio en el pensamiento Lean se extiende mucho más allá del desperdicio físico. Ron Mascitelli, experto en desarrollo de productos Lean, describe el desperdicio como “todo aquello con lo que el cliente no estaría de acuerdo en pagar” y los desarrolladores de software Lean, Mary y Tom Poppendieck, afirman que el desperdicio es “todo aquellos que no agregue valor al cliente”.
El TPS y la fabricación tradicional identifican siete tipos de residuos (o muda en japonés). Aunque estos tipos de residuos se crearon teniendo en cuenta la fabricación física del producto final, también se traducen en proyectos no físicos. Veamos los siete tipos de residuos y mostramos cómo se pueden interpretar fuera de la fabricación tradicional.
Siete áreas de desperdicio en Lean
Sobreproducción: Esta categoría, utilizada tradicionalmente para hacer referencia a los residuos generados por la fabricación Push, abarca la producción excedente y los grandes inventarios. La sobreproducción en proyectos de software también se refiere a crear un producto antes de establecer la demanda. La sobreproducción también puede referirse al error de proporcionar funciones, características o servicios que el cliente no está dispuesto a pagar, lo que significa que parte del trabajo realizado en el proyecto es innecesario o redundante.
En espera: Este término tradicionalmente se refiere al tiempo entre que un producto está listo para pasar a la siguiente etapa de un ciclo de producción y el producto se mueve realmente a la siguiente etapa. En la fabricación, la espera se produce debido a los procesos con cuellos de botella; en la gestión blanda de proyectos puede ampliar esa definición para incluir el tiempo que la información necesaria para pasar a la siguiente etapa no está disponible.
Transporte: Esto se refiere al costo incurrido y al tiempo dedicado a mover físicamente un producto de un lugar a otro, especialmente cuando se está produciendo. Los costos potenciales del transporte se extienden más allá del tiempo y el dinero gastado en el transporte en sí, ya que el transporte también plantea los riesgos de dañar los productos. La ineficiencia aumenta cuando los procesos de producción requieren que los bienes viajen innecesariamente más por las fábricas. El desperdicio de transporte es menos un problema en los proyectos de servicio, donde la comunicación es en su mayoría digital e instantánea. Pero los rastros de papel ineficientes y las fallas de comunicación, como interrupciones de energía o tiempos de inactividad de TI, siguen siendo problemáticos.
Exceso de procesamiento: En la fabricación, el exceso de procesamiento se refiere a hacer un trabajo que no es necesario. Esto podría ser pintar áreas que no se verán o tolerancias más estrechas de lo necesario. Esto impone costos relacionados con la mano de obra, los materiales y el desgaste del equipo. En los proyectos de servicio, el procesamiento excesivo adopta la forma de jerarquías y niveles de aprobación intrincados y redundantes, así como el escenario de desarrollo de software de crear más iteraciones de un producto de software de lo que realmente se necesitaba para obtener el valor del producto.
Inventario: En la fabricación, un enfoque Push puede resultar en un exceso de inventario, lo que genera desperdicios relacionados con el transporte y puede consumir espacio utilizable. El inventario también puede evitar la identificación de problemas con el flujo de trabajo. En los proyectos de servicio, los costos de inventario tienden a mitigarse, pero el almacenamiento excesivo de información y la dificultad para recuperar la información cuando es necesario son análogos.
Movimiento: Los desperdicios relacionados con el movimiento ocurren (en la fabricación, los proyectos duros y los proyectos blandos) cuando los trabajadores tienen que mover demasiado para realizar sus tareas económicamente. Una vez más, esto es un problema menor con el trabajo de conocimientos, cuando se puede extraer rápidamente los recursos digitales necesarios. Sin embargo, los recursos no digitales pueden constituir una proporción sustancial de recursos utilizados incluso en proyectos blandos, y la inaccesibilidad causa el movimiento desperdiciado.
Defectos: El problema de los defectos es similar para todo tipo de trabajo e implica volver a trabajar y utilizar más recursos de los que deberían haber sido necesarios. La diferencia radica en cómo se originan los defectos. En la fabricación, los defectos suelen ser causados por defectuosos del equipo o errores del operador, mientras que en el trabajo de conocimiento se derivan de un diseño deficiente o de una estimación inexacta.
La metodología Lean Six Sigma también se refiere a un octavo desperdicio: capacidad intelectual o habilidades subutilizadas. Este tipo de desperdicios se asocia principalmente con el trabajo del conocimiento y se refiere al desperdicio que se produce al no aprovechar todo el potencial mental de un trabajador. Esto puede ocurrir cuando las empresas contratan empleados sobrecalificados o colocan a los trabajadores en puestos en los que no pueden ejercer por completo sus habilidades.
Cómo Lean puede prevenir errores fatales del proyecto
Los principios lean y el reconocimiento de los residuos pueden ayudar a los gerentes de proyectos a evitar, mitigar o controlar situaciones que de otro modo podrían derivar en el fracaso del proyecto. A continuación, le mostremos una lista de los obstáculos comunes del proyecto que el pensamiento lean puede evitar:
No establecer el valor del cliente: No entender lo que un cliente valora en su proyecto puede hacer que valore incorrectamente el proyecto y que desperdicie trabajo y recursos. Al comprender el valor que su empresa ofrece a los clientes, puede establecer con mayor claridad los requisitos del proyecto, calcular el precio del proyecto según lo que un cliente está dispuesto a pagar y revisar los flujos de trabajo para cumplir con este precio objetivo.
Corrupción del alcance: La corrupción del alcance se produce cuando se aumenta el valor de un proyecto (por lo general, debido a las solicitudes de los clientes), pero los cambios correspondientes en el presupuesto y los precios no tienen en cuenta el valor aumentado. Puede evitar este problema al comprender y revaluar el valor para el cliente cuando se producen cambios en el alcance y asegurarse de que el aumento del valor vaya acompañado de un cambio en los precios.
No definir el flujo de valor: La asignación de flujos de valor es una excelente manera de ver cómo generan valor las actividades del proyecto y es esencial para recortar actividades que no crean valor para el proyecto. Si no asigna ni define el flujo de valor con la vista puesta en optimizarlo, las actividades que no crean valor pueden seguir forzando el presupuesto y ampliando el cronograma del proyecto.
Falta de compromiso de los participantes: En un mundo perfecto, los proyectos siempre terminaban a tiempo y nunca superaban el costo planificado. En realidad, la mayoría de los proyectos se ven afectados por los excesos de costos y cronogramas, por lo que contar con el respaldo total de los participantes es vital. Es menos probable que un participante que no esté completamente comprometido con el proyecto extienda el apoyo cuando un proyecto necesita sumergirse en sus reservas de contingencia o solicitar fondos de emergencia, lo que agrava drásticamente el problema de creación de residuos. Obtenga más información sobre cómo proteger y mantener el apoyo de las partes interesadas en La guía definitiva para la gestión de participantes.
Falta de un plan de comunicación: Un plan de comunicación eficaz optimiza el flujo de información entre los participantes de un proyecto. Sin una comunicación eficaz y oportuna, los proyectos corren el riesgo de desperdiciar tiempo y recursos en aprobaciones que requieren mucho tiempo, retrasos en el progreso y discrepancias de valor.
Tres metodologías populares de proyectos Lean
Ahora que comprendemos los principios del pensamiento lean, podemos ver cómo tres de las principales metodologías Lean (el ciclo de Deming, Six Sigma y Kanban) abordan la gestión de proyectos. Todos siguen un enfoque disciplinado de la gestión de proyectos, optimización del estrés del flujo de valor y asignan el flujo de valor en su estado actual. Después de identificar ineficiencias y desperdicios y realizar modificaciones, una asignación del estado futuro del flujo de valor establece el flujo de valor optimizado y rediseñado con un flujo mejorado. El estado futuro puede considerarse una etapa intermedia entre el flujo de valor tal como existe actualmente y un flujo de valor hipotético e ideal. Como tal, la asignación de flujos de valor es un proceso continuo, y las nuevas medidas para mejorar el flujo de valor se diseñan e implementan con regularidad.
A un nivel más granular, cada uno de los procesos que constituyen el flujo de valor se compone de una secuencia de pasos; se utilizan métricas para evaluar el rendimiento de estas secuencias. La aplicación de principios de gestión Lean dentro de los procesos de flujo de valor puede mejorar el rendimiento de estas métricas a escala microscópica y reducir el desperdicio a gran escala.
Recuerde que, independientemente de la metodología que use, los proyectos Lean exitosos buscarán mejorar continuamente el flujo a través del flujo de valor. Para ello, optimizan el flujo de información, examinan el flujo de valor y sus procesos constituyentes para las redundancias, y pretenden simplificar y estandarizar para reducir el desperdicio. En los proyectos de desarrollo, pueden adoptar un modelo de ciclo de vida que utilice el procesamiento simultáneo en un esfuerzo por mitigar los desperdicios causados por los cuellos de botella.
Un proyecto Lean también adoptará un enfoque Pull (en lugar de Push). Esto significa que el cliente reconoce la demanda del proyecto antes de que se ponga en marcha, y el proyecto se completa en respuesta a esta demanda. Dado que el pensamiento Lean es un concepto general, una organización que adopta los principios de gestión Lean, por lo general, habrá tenido éxito en la creación de una cultura de pensamiento lean entre sus empleados. Además, la gestión Lean asigna responsabilidades de toma de decisiones en toda la jerarquía de la empresa para minimizar el desperdicio causado por aprobaciones innecesarias y la burocracia. A menudo, esto significa confiar en los empleados de nivel inferior y empoderarlos para que tomen decisiones para las que están calificados, sin involucrarse en un proceso derrochador de revisión y aprobación.
El ciclo de Deming: Un método para la mejora continua de la calidad
El ciclo Deming, también conocido como resolución de problemas de A3 porque tradicionalmente se hacía en hojas de papel A3, toma su nombre de W. Edwards Deming, el consultor de gestión que ayudó a Japón a reconstruir sus capacidades de fabricación después de la Segunda Guerra Mundial. Deming, a quien a veces se conoce como “el padre del control de calidad”, creó el ciclo de Deming para facilitar la mejora constante de los procesos de negocios. El ciclo de Deming también se conoce como ciclo PDCA o ciclo PDSA (por planificar, hacer, verificar o estudiar y actuar).
Planning: la planificación implica conceptualizar y diseñar un plan para mejorar un proceso. Doing: hacer es implementar el plan y probar sus resultados utilizando métricas de rendimiento. Checking (verificar) o Studying (estudiar) implica determinar si el plan de mejora tuvo éxito, y Acting es la implementación permanente del plan para mejorar el proceso de negocios.
Existe cierto debate entre los gurús de la calidad sobre si PDCA y PDSA son lo mismo, pero generalmente cualquier distinción se considera demasiado pequeña para que el profesional promedio se preocupe.
La metodología del ciclo de Deming está orientada a abordar los problemas relacionados con los procesos con una única causa subyacente (o al menos una principal). Esta causa se denomina causa raíz y el equipo encargado de mejorar el proceso diseñará una o más soluciones posibles para abordar esta causa raíz.
Puede usar esta plantilla para llevar a cabo su propio análisis de causa raíz.
Descargar plantilla de análisis de causas raíz
Los profesionales también identifican la situación actual, o el estado actual del proceso, para determinar cómo abordar mejor la causa raíz e identificar cómo cambiar el proceso para abordar la causa raíz. Una vez que identifique y aborde la causa raíz, el equipo preparará una declaración de problemas que defina lo que están tratando de lograr y establezca la métrica para medir las soluciones. Estas soluciones se evalúan durante las fases de hacer y verificar. Después de realizar un análisis de costos y beneficios para determinar la solución óptima, el equipo recomienda un plan de acción al responsable de la toma de decisiones.
Para llevar a cabo su propio análisis A3, utilice esta plantilla de informe.
Descargar plantilla de informe A3
El ciclo de Deming: Ejemplo de proyecto en educación
La American Society for Quality cita como ejemplo de proyecto de ciclo de Deming el distrito escolar de Pearl River NY, que utiliza la técnica para el diseño del plan de estudios e instrucción.
La planificación del distrito escolar implica el análisis de las necesidades de los alumnos para identificar brechas o áreas de mejora en la instrucción. Hacer es un proceso de dos pasos que implica primero elaborar un plan de estudios que cumpla con los estándares estatales y nacionales y con las propias necesidades de los alumnos y, luego, proporcionar realmente la instrucción. La comprobación implica el uso de evaluaciones escolares para evaluar el rendimiento de los alumnos con el nuevo modo de instrucción. Por último, actuar es la implementación de planes de estudios y métodos instructivos que satisfacen con éxito las necesidades de los alumnos.
“Durante el año escolar, si las evaluaciones muestran que los alumnos no están aprendiendo según lo esperado, se realizan correcciones a mitad del curso, como la reinstrucción, el cambio de los métodos de enseñanza y la tutoría más directa de los docentes. Los datos de evaluación se convierten en aportes para el siguiente paso del ciclo”, señala el estudio de caso.
Six Sigma: Método basado en datos para eliminar defectos
Six Sigma es una metodología de mejora de procesos que se centra en eliminar los defectos y minimizar la variación en el resultado del proceso. Está fuertemente basado en datos. El nombre Six Sigma es una referencia estadística de que seis desviaciones estándar caen entre la media del proceso y el límite de especificación más cercano, lo que da como resultado una tasa de error de 3,4 defectos por millón de productos o resultados del proceso. Como tal, el objetivo principal de Six Sigma es optimizar la consistencia y precisión de un proceso. Puede leer una guía completa de Six Sigma aquí.
Six Sigma fue desarrollado por ingenieros de Motorola a mediados de la década de 1980 y, luego, Motorola registró el nombre. La técnica se convirtió en una piedra angular del enfoque del director ejecutivo de General Electric, Jack Welch, en la década de 1990. Es importante tener en cuenta que si bien Six Sigma y Lean no son lo mismo, la filosofía de gestión y la metodología se complementan muy bien. Lean modifica los procesos para eliminar residuos, y Six Sigma modifica los procesos para mejorar la calidad y la consistencia de la producción. Como tal, ambos juegan roles importantes en el rediseño de procesos. La metodología Six Sigma persigue la mejora de procesos a través de proyectos de mejora de Six Sigma, que adoptan una de las submetodologías Six Sigma. Analizaremos dos de estas submetodologías: DMAIC y DMEDI.
DMAIC: Este acrónimo (definir, medir, analizar, mejorar, controlar) se utiliza en proyectos de Six Sigma que tienen como objetivo renovar o mejorar un proceso de negocios existente. La fase de definición implica definir el alcance del problema que debe examinarse, establecer los requisitos del cliente y establecer objetivos para el proyecto. La medición es la evaluación del estado actual del proceso mediante la recopilación de datos. El análisis es el proceso de examen de los datos recopilados para identificar la causa raíz. La mejora implica el uso de técnicas de mejora del proceso para optimizar el proceso, lo que lo traslada a su futuro estado. Por último, el control implica supervisar el proceso nuevo y futuro para garantizar la calidad de la producción. Puede repetir DMAIC hasta que alcance el nivel deseado de uniformidad de calidad.
Descargar plantilla de análisis de causas de raíz de la Six Sigma DMAIC
DMEDI: Este acrónimo (definir, medir, explorar, desarrollar, implementar) se utiliza en proyectos Six Sigma que tienen como objetivo diseñar un nuevo proceso. Es menos basado en datos y más creativo que DMAIC. La fase de definición en DMEDI es similar a la de DMAIC: definir el proceso a diseñar y los objetivos del nuevo proceso. La medición es la identificación de los clientes y sus requisitos. La exploración es el proceso de examen de diseños de procesos alternativos para evaluar cuáles serán los que mejor se adapten a los requisitos de los clientes. El desarrollo es la producción real del diseño que se considera óptima para satisfacer los requisitos del consumidor. Por último, la implementación implica realizar pruebas piloto del nuevo proceso para garantizar que su producción cumpla con los requisitos de los clientes.
La decisión de usar DMAIC o DMEDI depende realmente de evaluar el estado de un proceso, si existe en absoluto. El pensamiento convencional dice que el DMAIC se utiliza para mejorar un proceso existente, y el DMEDI para establecer un proceso nuevo. Sin embargo, en algunos casos, un proceso existente puede estar tan lleno de problemas y causas raíz que es más fácil diseñar un proceso nuevo que intentar mejorar el existente. Si este es el caso, el DMEDI puede ser una mejor opción que DMAIC.
Six Sigma utiliza un sistema de cinturón al estilo de las artes marciales para indicar los niveles de certificación. Los cinturones, en orden de aumento de la experiencia, son: Cinturón blanco, cinturón amarillo, cinturón verde, cinturón negro y cinturón negro maestro. Los cinturones negros y cinturones negros maestros lideran proyectos de resolución de problemas de Six Sigma y capacitan a otros que buscan la certificación Six Sigma. Obtenga más información sobre la certificación Six Sigma aquí.
Lean Six Sigma: La combinación de enfoques en el desperdicio, la calidad
Lean Six Sigma es una metodología de mejora de procesos que se une a los principios de reducción de residuos de Lean con los esfuerzos de mejora de la calidad de Six Sigma. El profesional de gestión del rendimiento Arun Hariharan explica que puede clasificarse a los proyectos Lean Six Sigma en tres categorías generales:
- Los proyectos de mejora de la calidad dependen principalmente de los métodos Six Sigma para mejorar la calidad de los procesos.
- Los proyectos que mejoran los ingresos dependen igualmente de Six Sigma y Lean para mejorar la calidad, reducir el desperdicio (aumentando así la velocidad) y, por lo tanto, aumentar los ingresos de la empresa.
- Los proyectos de ahorro de costos dependen principalmente de los principios Lean para reducir el desperdicio de un proyecto, lo que lo hace más rápido, eficiente y, por lo tanto, más barato.
Six Sigma: Ejemplo de proyecto de fabricación médica
Tal vez el proyecto más emblemático de Six Sigma sea el que se llevó a cabo en Motorola a fines de la década de 1980, cuando los ingenieros de Motorola que querían aumentar la granularidad en la medición de la calidad pasaron de medir defectos por cada mil oportunidades a defectos por millón de oportunidades. Este cambio en la forma de analizar y percibir la calidad eventualmente conduciría a más de $16 000 millones en ahorros para la empresa a través de mayor precisión y conformidad con los requisitos de calidad. Desde entonces, los métodos Six Sigma y Lean Six Sigma se han implementado en miles de organizaciones en los EE.UU., incluidos Ford, General Electric y el ejército de los Estados Unidos.
Otro ejemplo de los beneficios de Six Sigma es Orchid, un fabricante de articulaciones artificiales utilizadas en reemplazos de cadera y rodilla, entre otros productos. Su proceso implica la fundición de moldes con cera pérdida que se utilizan para formar la articulación artificial de cobalto. La empresa descubrió que el seis por ciento de sus moldes se agrietarían, desperdiciando el cobalto.
Un equipo de Six Sigma, incluido un recepcionista de plantas, comenzó a investigar el problema alrededor de 2010. Identificaron 200 variables en el proceso de fabricación que especularon podrían contribuir a los moldes agrietados. El recepcionista notó que había dos tipos de cera empleadas en la fundición, la cera virgen para las partes que estarían en contacto con las superficies implantadas en el paciente y la cera recuperada para las piezas sin contacto.
Las pruebas realizadas por el equipo de Six Sigma descubrieron que las ceras se fundían a diferentes temperaturas, lo que podía explicar el agrietamiento. Trataron de verificarlo con 100 piezas de fundición utilizando solamente cera virgen. En esa prueba, no se rompió ni un solo molde. Dieciséis años antes, la empresa había empezado a usar la cera regenerada para ahorrar 60 centavos por libra sobre la cera virgen, pero la decisión estaba causando desperdicios de cobalto que costaban entre $7,50 y $15 la libra. El paso a la cera virgen, una variable identificada a través de los métodos Six Sigma, ahorró a Orchid un estimado de $2,1 millones al año.
Kanban: Limitar el trabajo en curso para acelerar la finalización
Kanban es otro método Lean que se originó en Toyota. Esta metodología se centra en eliminar los backlogs del trabajo en curso y mantener el trabajo fluyendo sin problemas. Para leer cómo usan Kanban las empresas de fabricación y software, consulte esta referencia.
En una fábrica ideal, el trabajo avanzaba a un ritmo constante, a veces denominado flujo continuo, y nunca se vería objeto de cuellos de botella. Sin embargo, en realidad algunos procesos son más lentos que otros, y si estos procesos son de comercialización de procesos más rápidos, causan backlogs. Los backlogs ocupan espacio y su almacenamiento cuesta dinero y pueden ocultar problemas como defectos de calidad. Obtenga más información sobre Kanban en la gestión de inventario aquí.
Toyota solucionó este problema mediante la implementación de un sistema de señales visuales (tarjetas llamadas tarjetas Kanban) para indicar cuándo estaba disponible un proceso para asumir nuevos trabajos. Como tal, el ritmo de trabajo se establece por el eslabón más lento de la cadena de producción, que "tiraría" de la producción utilizando señales de tarjeta para indicar cuándo estaba disponible para procesar el trabajo. Como se ha comentado anteriormente, el enfoque Pull limita el backlog y controla los cuellos de botella para reducir el desperdicio. Kanban también limita la cantidad de elementos que se procesan en cualquier momento.
El sistema Kanban clásico es un tablero dividido en secciones, con una serie de tarjetas móviles. Cada sección representa un proceso en particular, y las tarjetas individuales representan los elementos de trabajo que se mueven a través de estos procesos. Las señales visuales facilitan la detección de ineficiencias y backlogs, por lo que Kanban puede ser una excelente manera de identificar los procesos de mejora.
Dado lo fácil y efectivo que es de usar, Kanban es ampliamente adoptado por organizaciones y equipos de todos los tamaños que ejecutan líneas de producción de varios procesos. Kanban también es ideal para el trabajo de conocimientos, como la publicación de contenidos, que implica varios procesos (redacción, edición, corrección y composición tipográfica e impresión). Al usar tarjetas para simbolizar piezas individuales de contenido, puede realizar un seguimiento del progreso a través de la cadena editorial y de diseño, y asignar recursos humanos cuando se desarrollen backlogs. Se muestran las tarjetas están en un tablero Kanban; tradicionalmente esto era un tablero de boletines físicos, pero hoy en día suele crearse en línea.
Kanban se ha vuelto popular en los servicios y el trabajo del conocimiento. Cuando se aplican a estos proyectos, los principios básicos son:
- Visualizar el trabajo
- Limitar el trabajo en curso
- Los equipos sacan trabajo cuando han completado las tareas existentes
- Sin sprints (intervalos de trabajo basados en el tiempo)
Ejemplo de proyecto Kanban: El sitio web cosecha eficiencias
Un ejemplo impresionante del éxito de Kanban proviene de Moneysupermarket.com, un sitio web de comparación y compras en el Reino Unido que presta servicio a más de 120 millones de usuarios al año. El equipo de desarrollo estaba sufriendo una alta demanda, cambiando constantemente las prioridades, la moral deficiente y el bajo rendimiento. El uso del tablero Kanban resaltó los cuellos de botella y los obstáculos obvios y dejó en claro dónde debía centrarse el equipo para abordar los problemas.
Después de implementar Kanban, el plazo de entrega del equipo se redujo de 120 días a 25 días y el rendimiento se disparó. Los desarrolladores eliminaron el backlog de 469 trabajos en cinco meses.
Implementación de Lean: Consejos para hacer que Lean le funcione
Al implementar Lean, lo más importante que hay que recordar es que se emplea mejor como filosofía a largo plazo, en lugar de una solución rápida a problemas relacionados con el desperdicio. La reducción de residuos es un proceso continuo, y el desarrollo de una filosofía de pensamiento Lean y una medición uniforme del rendimiento garantiza beneficios mayores y sostenidos con el tiempo. También facilita la aplicación de los principios Lean ya que los trabajadores aprenden a reconocer el desperdicio a través de la práctica.
Uno de los objetivos finales de Lean es crear y mantener un flujo continuo de procesos, donde el trabajo se mueve a través de los subprocesos sin parar y crear desperdicios. Para ello, las organizaciones implementarán enfoques Pull, lo que reduce drásticamente los costos de inventario, almacenamiento y mantenimiento al producir productos finales a demanda. A largo plazo, este enfoque Pull conduce a una distribución del trabajo más uniforme, que puede mitigar los problemas asociados a la sobrecarga de trabajo, tanto para las máquinas como para las personas.
Por supuesto, Lean también reconoce que el flujo puede ser interrumpido no solo por los procesos de producción, sino también por el flujo de información. Fomentar una cultura de comunicación sólida y rápida es esencial para el éxito de la gestión Lean. La implementación de herramientas que facilitan la comunicación, como Kanban, suele ser un suplemento necesario para agilizar y mejorar los flujos de trabajo.
Para incorporar los principios de la gestión Lean, comience con proyectos pequeños y bien definidos entregados a plazos cortos. Esto es útil por varias razones. Por un lado, enseña a las personas a reconocer el desperdicio y a decidir qué hacer al respecto. Además, tiene el potencial de aportar beneficios rápidos gracias a la reducción de desperdicios. Dado que suelen ser más inmediatos para los proyectos cortos, esto puede hacer maravillas para los gerentes de proyectos que intentan desarrollar una cultura de pensamiento Lean en un equipo de proyecto.
Los gerentes de proyectos también deben defender el principio básico Lean de mejora continua (Kaizen) con respecto a sus empleados y equipos. Fomente la capacitación y el aprendizaje continuos, y los gerentes de proyectos pueden obtener certificaciones en gestión de proyectos Lean, como las que ofrecen Villanova University y Management and Strategy Institute.
Las mejores herramientas para gerentes de proyectos Lean
Los gerentes de proyectos Lean han desarrollado algunas herramientas para ayudar en la gestión de proyectos y la transformación organizativa. Algunas de estas herramientas son marcos conceptuales o de procesos, mientras que otras existen como software y sistemas.
Asignación de flujo de valor: Como hemos comentado, el mapa de flujo de valor traza el flujo de materiales e información involucrados en la creación de un producto. Utilice un mapa de flujo de valor para analizar el estado actual de un flujo de valor y para diseñar mejores estados futuros que eliminen los desperdicios y creen valor según las demandas de los clientes. Tradicionalmente, la asignación de flujos de valor se hacía en papel, pero ahora también existen herramientas en línea disponibles.
Celdas de trabajo: En la fabricación, una celda de trabajo es una disposición estratégica de recursos diseñada para mejorar el flujo de un proceso y disminuir el desperdicio. Puede crear acuerdos de celdas de trabajo utilizando equipos físicos o recursos humanos y, a menudo, una combinación de ambos. Un equipo interdisciplinario es un ejemplo de una celda de trabajo basada principalmente en recursos humanos, mientras que la fabricación de espacios de trabajo es un ejemplo de celdas de trabajo centradas en el equipo físico.
Flujo de una pieza: El flujo de una pieza es la práctica de mover elementos de trabajo a través de una celda de trabajo de una pieza a la vez (en lugar de por lotes) y se hace principalmente para disminuir el trabajo en curso. Procesar un elemento de trabajo a la vez es más rápido que hacer que cada trabajador produzca lotes de trabajo antes de moverlos al siguiente paso (ya que los lotes tardan más en procesarse que un solo elemento y el trabajo no puede pasar a la comercialización hasta que se finaliza todo el lote).
Kaizen: Llamado así por una palabra japonesa que se traduce aproximadamente como "buen cambio", Kaizen es un enfoque del trabajo que pone énfasis en las mejoras incrementales en los procesos y flujos de trabajo. Los objetivos finales de Kaizen son mejorar la eficiencia y la calidad. El concepto alienta a una organización a acoger mejoras pequeñas y fáciles de implementar que, en conjunto, aportan grandes beneficios a largo plazo. Una forma popular de implementar Kaizen es comenzar con un evento Kaizen, un proyecto a corto plazo (alrededor de una semana) con un único objetivo específico de mejora. Un plan común para un evento Kaizen (también a veces llamado Kaizen Blitz) asigna una función para cada día, como la documentación del estado actual, la evaluación del estado actual, la caracterización del estado futuro, la implementación del estado futuro y la puesta en práctica del estado futuro.
Para ejecutar su propio evento Kaizen, use esta plantilla para realizar un seguimiento de su trabajo.
Descargar plantilla de resultados de eventos de mejora rápida lean (Kaizen)
5S: Un método de organización del espacio de trabajo que organiza los recursos relacionados con el trabajo de una manera que facilita el trabajo eficiente y eficaz. El nombre 5S proviene de cinco palabras en japonés que, traducidas al español, significan clasificar, ordenar, relucir, estandarizar y sostener. 5S se utiliza comúnmente en Lean Six Sigma como una metodología para organizar los lugares de trabajo y utilizar señales visuales para lograr resultados más consistentes. Los pasos involucrados son eliminar elementos que no son necesarios para las operaciones actuales, etiquetar y organizar los elementos para que sean fáciles de usar, mantener todo ordenado todos los días, estandarizar un sistema para mantener las cosas en orden y evitar la reincidencia. Si bien este sistema comenzó en fábricas, es igualmente relevante para las oficinas. Pruebe esta lista de verificación 5S en su lugar de trabajo.
Descargar plantilla de lista de verificación de 5S para oficinas
Poka yoke: Un mecanismo para la prueba de errores. Ayuda a los operadores humanos a identificar, prevenir o corregir errores a medida que ocurren. La idea detrás de Poka Yoke es tener en cuenta los defectos a medida que ocurren y minimizar el desperdicio que de otro modo se causaría si los defectos avanzaban por la cadena de producción. Por lo general, Poka Yoke se dividen entre los mecanismos de control y advertencia. Un ejemplo de control Poka Yoke son conectores eléctricos diseñados para que solo encajen de la manera correcta. En un sentido más amplio, Poka Yoke puede ser cualquier técnica que ponga a prueba la seguridad de un proceso para que no se pueda arruinar.
Gemba Walk: Gemba Walk es una aplicación del principio de observar el trabajo a medida que se produce y donde se produce. Es un complemento del proceso Kaizen y se basa en la idea de que los procesos de trabajo se observan mejor y, por lo tanto, se mejoran en tiempo real y en el entorno de trabajo real. Gemba, a veces descrita como "gestión al caminar", es más que un gerente que se pasea por la oficina y supervisa el trabajo. En Lean, el propósito de Gemba es observar, involucrar y mejorar, y debe ocurrir donde se produce la actividad más crítica (la línea de producción en fabricación, el aula de educación, etc.). Sus interacciones están diseñadas para involucrar a las personas y los procesos en Kaizen o mejoras continuas e incrementales.
Obeya Room: Obeya Room, o "sala de guerra", es un gran espacio físico que se utiliza durante el desarrollo de un producto o proceso nuevo para facilitar el pensamiento y la comunicación interdepartamentales. Todas las personas involucradas en el proceso de desarrollo se reúnen en la Obeya Room para comunicarse y tomar decisiones sobre un proyecto específico. Por lo general, la Obeya Room está equipada para facilitar la discusión y la resolución de problemas, y acelerar la toma de decisiones.
Señales visuales: La premisa básica de Kanban es que es más fácil entender y ejecutar procesos visualmente que solo con palabras o números. Como tal, el uso de señales visuales al estilo Kanban (notas adhesivas, pelotas de golf de colores, gráficos de control visual o herramientas de software que representan elementos de trabajo visualmente) es una forma probada de simplificar y acelerar la comunicación, así como de facilitar la comprensión de un proceso.
Documentar las métricas y el progreso: Dado que el pensamiento lean, en última instancia, se refiere a reducir el desperdicio y mejorar el flujo (y, por lo general, lo intenta de manera gradual), es fundamental definir métricas que midan el flujo y registrar constantemente el rendimiento de dichas métricas. Por ejemplo, puede evaluar el flujo por medio de métricas como el trabajo en curso, el plazo de entrega, el tiempo de espera y el rendimiento. Lo mejor para medir estas métricas es usar herramientas de software, que pueden determinar y visualizar rápidamente el rendimiento a través de gráficos o estadísticas resumidas.
Cómo se relaciona Lean con los métodos Agile
En el desarrollo de software, existe una tendencia a confundir los principios del pensamiento Lean con las metodologías del manifiesto Agile. Entonces, ¿cuán similares son?
Las metodologías Agile son un conjunto de enfoques de desarrollo iterativos diseñados específicamente para satisfacer los requisitos de los clientes en constante cambio en los proyectos de desarrollo de software. La característica de firma de un proyecto Agile es su alcance flexible, lo que significa que las metodologías Agile están diseñadas para aceptar e implementar fácilmente los cambios en los requisitos. El desarrollo de software Agile consta de una serie de iteraciones y los equipos de desarrollo de software Agile se enfocan en mejoras incrementales en cada iteración.
Hay algunas similitudes entre la gestión de proyectos Agile y Lean. Ambos priorizan la satisfacción del cliente: Agile a través de extensos comentarios e iteraciones de clientes, y Lean al identificar el valor a través de los ojos del cliente. Ambos también se centran en la mejora incremental, en lugar de grandes correcciones únicas.
La gestión de proyectos Lean y Agile también son similares en otros aspectos:
- Adoptar una cultura de participación de los empleados sin culpas que garantice la aceptación de la filosofía Lean y contribuya a la eficiencia de las metodologías Agile
- El rol de un facilitador o líder de proyecto sólido para garantizar que el proyecto se mantenga encaminado y aplica de manera eficaz los principios de Lean o Agile
- Eliminación de residuos o trabajo redundante, y la sustitución o el rediseño de procesos ineficientes
- La práctica de canalizar los proyectos para garantizar la entrega continua de proyectos
Sin embargo, en otras formas fundamentales, Lean es muy diferente de Agile:
- Lean es una filosofía de negocios extensa y de gran alcance que está diseñada para mejorar la eficiencia de los procesos y, al mismo tiempo, eliminar el desperdicio. Se traduce en mejoras en los procesos que duran largos períodos y que beneficiarán a futuros proyectos. Por el contrario, Agile es simplemente un método para garantizar que los requisitos de un cliente para un proyecto discreto se cumplan de manera rápida y eficiente.
- Los principios Lean funcionan mejor cuando se aplican en toda una organización, fomentando la eficiencia general y mejorando todos los sistemas de procesos. En cambio, la metodología Agile se aborda la toma de decisiones rápidas y buenas dentro de los proyectos de desarrollo y no se aplica fuera del trabajo del proyecto.
Gestión Lean en todos los sectores
Los principios básicos del pensamiento Lean pueden beneficiar a muchas industrias y tipos de proyectos. A continuación, incluimos algunos ejemplos de la gestión Lean en acción:
Lean aporta una mayor eficiencia en la atención médica
Como señala Daniel T. Jones, uno de los autores de The Machine that Changed the World y Lean Thinking: la aplicación de los principios de gestión Lean en la atención médica puede “ofrecer una mejor calidad (y seguridad) y una mejor experiencia del paciente (menos filas y trabajos duplicados) y, al mismo tiempo, hacer un mejor uso de los recursos existentes (para tratar a más pacientes) y mejorar la experiencia laboral del personal (menos frustración y estrés)”. Afirma que esto es vital en un momento en que los sistemas de atención médica de todo el mundo enfrentan un creciente estrés.
Los hospitales son un entorno extremadamente desafiante pero gratificante para Lean. Son un conjunto típicamente complejo de procesos interconectados, que van desde las admisiones hasta la atención del paciente hasta la gestión de instalaciones costosas y delicadas y la coordinación de los suministros médicos. Reducir constantemente el desperdicio conduce, a largo plazo, a operaciones más eficientes en términos de costos y tiempo, y, en general, a una experiencia más agradable para los pacientes.
Esta ficha técnica del Institute for Healthcare Improvement detalla el éxito de la gestión Lean en el Virginia Mason Medical Center en Seattle, Washington. Al eliminar el desperdicio, Virginia Mason incrementó la capacidad de su programa y ahorró millones de dólares en instalaciones ampliadas que ya no eran necesarias. También lograron reducir la cantidad de equivalentes a tiempo completo a pesar de una política de no despidos, debido a la mejora de los procesos que aumentaron la productividad y, por lo tanto, redujeron la necesidad de sustituir al personal jubilado. El centro también vio disminuciones notables en los tiempos de configuración y entrega, el espacio utilizado y las distancias recorridas.
Servicios financieros: Menos errores, procesamiento más rápido
El sector financiero, en general, tardó en adoptar los principios de la gestión lean. Sin embargo, la crisis económica de 2008 acarreó la importancia de la reducción de costos simplemente para que las instituciones financieras pudieran sobrevivir. Como tal, un creciente número de instituciones financieras están recurriendo a la gestión Lean y descubriendo problemas bastante graves de eficiencia y desperdicio en el proceso.
Dado que las instituciones financieras utilizan el servicio al cliente para diferenciarse de la competencia, los pensamientos Lean se centran en el valor a los ojos del cliente ha demostrado ser valioso. Los bancos se han centrado en reducir los tiempos de atención al cliente. También son capaces de ofrecer un precio más atractivo de los productos al reducir los servicios que no aportan valor. En el back-end, los bancos ven las mejoras esperadas en la eficiencia y los costos de ejecución, así como una disminución de los tiempos de procesamiento para las operaciones que no deberían demorar tanto en finalizarse.
Al usar Lean, los bancos suelen ver entre 15 y 25 mejoras en la eficiencia, según Boston Consulting Group. Un banco pudo procesar las transacciones con un 30 por ciento más de eficiencia y, a la vez, mejorar la satisfacción de los clientes con Lean y un gerente de activos de América del Norte hizo que los precios de los productos fueran entre un 12 y un 20 por ciento más eficientes. Según McKinsey, un banco global de inversiones redujo las imprecisiones en un 50 por ciento y mejoró el cronograma y la productividad en un 40 por ciento cada uno.
Minorista obtiene las principales tendencias en manos de los compradores con Lean
Los principios Lean ayudan a los minoristas a cumplir con el desafío perenne de la gestión de inventarios. Tradicionalmente, a las tiendas minoristas les resultaba difícil mantener los estantes abastecidos de artículos que los clientes quisieran y perder en las ventas potenciales cuando no pueden hacerlo. La solución a este desafío es un enfoque Justo a tiempo (JIT) similar al utilizado en la fabricación Lean. Esto significa optimizar, coordinar y programar el transporte y la manipulación y reducir los costos de inventario. En el extremo orientado al cliente, la gestión Lean puede mejorar la experiencia de compra reduciendo los tiempos de espera, liberando a más personal para ayudar a los clientes y asegurando que los clientes puedan encontrar lo que quieren. Y, por supuesto, los costos más bajos que conlleva el aumento de la eficiencia pueden traducirse en precios más atractivos, lo que a menudo es el resultado para los clientes minoristas.
La minorista de moda rápida Zara utilizó el pensamiento Lean para convertirse en uno de los minoristas más lucrativos del negocio. Entre las prácticas inspiradas en la metodología Lean de Zara, la fabricación JIT permite bajas existencias de inventario y una actualización rápida de las líneas de productos, lo que retrasa el compromiso con diseños particulares hasta que se establece la preferencia de diseño del cliente, el uso de métodos Agile para diseñar rápidamente artículos de moda según las preferencias de los clientes y el uso de Kanban y One Piece Flow para satisfacer la demanda de los clientes con rapidez y precisión.
Las herramientas Lean ayudan a los educadores a impulsar los logros académicos
La adopción del pensamiento Lean fue lenta en el sector de la educación pública, pero ahora hay una creciente apreciación de lo que los principios Lean pueden aportar a la educación.
Tal vez la aplicación más fascinante de los principios lean en la educación se refiere a la función central de la educación: ayudar a los alumnos a aprender. Los debates pedagógicos se apoderan de las formas más eficaces de hacerlo, lo que significa que un enfoque sistemático e inspirado en la metodología Lean para identificar técnicas pedagógicas menos eficaces (y reconocer las más eficaces) puede ayudar a estandarizar las mejores prácticas de enseñanza. El pensamiento Lean podría ayudar a eliminar las diferencias en la educación y beneficiar a los alumnos de todas partes.
Lean Enterprise Institute informa sobre el éxito del pensamiento Lean en mejorar los logros académicos en las escuelas públicas de Columbus, Ohio. Con herramientas Lean como la asignación de procesos y la asignación de flujos de valor, las escuelas impulsaron los logros académicos al reducir el tiempo entre las pruebas y la revisión de los materiales de las pruebas para garantizar que los alumnos aprendieron y reforzaron los conceptos de manera más eficaz. Los directores de escuela adoptaron un enfoque más estandarizado para registrar y compartir las observaciones en el salón de clases, detectando las tendencias macro en el proceso. La aplicación del sistema de organización del espacio de trabajo 5S ayudó a optimizar los procesos en las oficinas de los directores y secretarios.
La construcción Lean ayuda a los bebés enfermos a irse a casa más rápido
Lean Construction Institute (LCI) ve la entrega Lean como una forma de responder a la insatisfacción de los clientes y de la cadena de suministro con la industria de la construcción. El LCI cita la disminución de la productividad y la eficiencia en la industria de la construcción como impulsor hacia los enfoques Lean y utiliza su sistema Last Planner System registrado para reducir la variabilidad del flujo de trabajo para que los proyectos sean más predecibles y la coordinación sea más sencilla. La construcción Lean, tal vez la aplicación exclusiva del pensamiento Lean en la gestión de proyectos, se centra en los principios básicos de lean para definir el valor del cliente, maximizar el valor y minimizar el desperdicio, adoptar un enfoque Pull, buscar el flujo continuo y empoderar a los participantes del proyecto con información y autoridad descentralizada para la toma de decisiones.
Como ejemplo de los principios de construcción Lean en acción, en la Ambulatory Surgery & Critical Care Tower de Akron Children’s Hospital en Akron, Ohio, diversos participantes, incluidos constructores, arquitectos, médicos, enfermeras, pacientes y sus familias participaron en el proceso de diseño. Esto permitió a los propietarios del proyecto medir el valor desde las perspectivas de varios "clientes”. Las simulaciones realistas de las instalaciones basadas en estos diseños se probaron repetidamente y luego se rediseñaron en función de los comentarios.
Por ejemplo, Akron Critical Care Tower construyó habitaciones privadas para las nuevas madres y sus bebés basándose en la evidencia de que los recién nacidos en estado crítico mejoran lo suficiente como para regresar a casa más rápido. Al debatir sobre las formas más eficaces y eficientes de localizar y diseñar instalaciones, almacenar equipos y suministros, y albergar a los pacientes mientras se cumplen las metas de costo objetivo, los diseñadores redujeron la superficie de referencia en hasta un 20 por ciento en cada planta.
Por qué Smartsheet es una herramienta útil para la gestión de proyectos Lean
De la administración básica de tareas y de proyectos hasta la administración compleja de recursos y portafolios, Smartsheet lo ayuda a mejorar la colaboración y acelerar el trabajo. Esto lo empodera para lograr más. La plataforma Smartsheet facilita la planificación, la captura, la gestión y la creación de informes sobre el trabajo, desde cualquier lugar, lo que ayuda a su equipo a ser más eficiente y lograr más. Cree informes sobre las métricas clave y obtenga visibilidad en tiempo real acerca de trabajo gracias a informes, paneles y flujos de trabajo automatizados diseñados para ayudar a su equipo a mantenerse conectado e informado. Cuando los equipos tienen claridad sobre el trabajo en curso, pueden lograr mucho más en menos tiempo. Pruebe Smartsheet gratis hoy mismo.